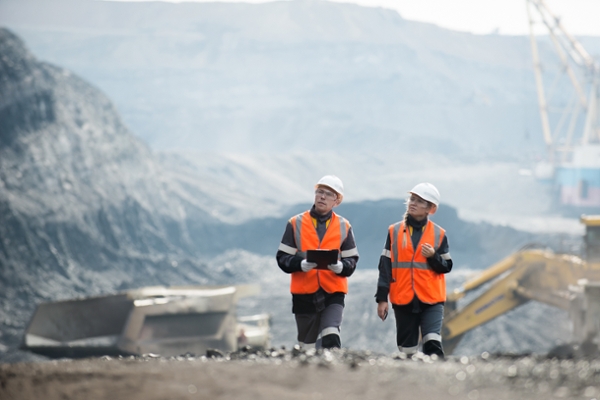
Innovation, Disruption and The Second Economy of Mining
The global mining industry, like so many other economic sectors, is in the midst of a technological revolution. What has long been considered a mature industry is going through a wave of technology-driven disruption. So transformational are the changes that there is not even useful language to capture the scope of what is taking place.
By Brian Wixted, Adjunct Professor, Johnson Shoyama Centre for the Study of Science and Innovation Policy, University of SaskatchewanThe global mining industry, like so many other economic sectors, is in the midst of a technological revolution. What has long been considered a mature industry is going through a wave of technology-driven disruption. So transformational are the changes that there is not even useful language to capture the scope of what is taking place.
For example, “robot mines” is only suggestive of perhaps artificial intelligence and heavy equipment, but not the potential for big-data activities to fine-tune operations. Cyber mines, on the other hand, suggest “data mining”, but not traditional blasting rock. Thus, economist Brian Arthur’s1 term the “second economy” is perhaps the most evocative. As many of the elements of this ‘second economy’ are not yet present in Canada, this policy brief brings together the evidence on the leading edge of change from Australia to highlight what we might see over time in Canada.
As is always the case with the application of new technology, in some parts of the world there is a technological revolution underway. In other regions, companies are waiting to see if the technologies are robust in difficult environments and whether the business strategies pay off.
But, before we can start to interpret the change, we need a mind shift. To do that requires we divert our attention from minerals and commodities to the mining technologies. Traditionally, statistics have not been developed to make such an analysis easy. Back-of-the-envelope calculations could be possible, but perhaps that is a project for the future. The point is, mining technologies differ whether the extraction method is drilling, underground activities or open-pit activities. For example:
- Drilling based operations (particularly oil and gas) are deploying data and visualisation tools;
- Open-pit mines are using autonomous heavy machinery; and
- Underground miners have found the conditions more difficult to develop and apply advanced new technologies—although at the leading edge there is transformation here as well.
This Policy Brief focuses on developments in Australia, which is considered a global leader in technological innovation in mining. While Canada is also embracing robotic mining and other advanced technologies, it is not as advanced as Australia. As concluded by Canada’s Economy Strategy Table that addressed the resource sector, Canada has shown a “lack of agility in technology adoption.”2
Our core interest in this paper is identified in the following table.
Table 1: Areas of Interest
Processing Time | Extraction Approach | ||
OPEN PIT | UNDERGROUND | DRILLING | |
Exploration | |||
Mining | |||
Processing | |||
Mining Services (software) |
The most “sci-fi” like technologies are appearing in the open-pit mines in Australia’s western iron ore mines and eastern coal fields. A leader in technological innovation is the Anglo-Australian mining giant Rio Tinto, which is a global leader in the application of cutting-edge mining automation. Rio’s automation efforts are broad-ranging, under what it labels the ‘Mine of the Future’ project.
Trucks (automated haulage)
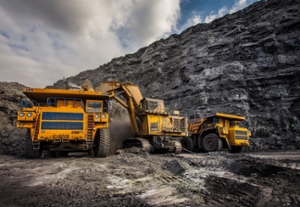
The first technology of significance is the haul truck, the workhorse of the mine, which can be anywhere up to 400 tonnes gross weight. The media have struggled to understand the difference between remote-controlled, ‘robot’ and ‘autonomous’. The available evidence suggests the equipment is autonomous, although monitored from 1,200km away in Perth. That is, they are self-driving and can determine when to stop and manoeuvre independently of an overseer in Perth.
The timeline of change has been remarkably swift. Rio Tinto first introduced 12 Komatsu haul trucks for trial in 2008. By 2014 it had 30 working in the iron ore mines of Australia’s north-west Pilbara region3. By 2015 it was being reported that “The first two mines in the world to start moving all of their iron ore using fully remote-controlled trucks have just gone online in Western Australia’s Pilbara”4.
More recent information suggests that Rio Tinto has 76 autonomous haul trucks, BHP has probably 50 at the end of 2017 and Fortescue Metals Group is aiming for 168 driverless trucks5. The evidence is that similar equipment is in Australia’s east coast open-pit coal mines being operated by BHP, but numbers for the equipment is less readily available.
Suncor in Canada (2018) has ordered 150 similar machines, appearing to jeopardize 400 jobs6.
Rio’s “mine of the future”7 continues to evolve with the development and deployment of an extensive range of autonomous equipment.
Drilling Rigs
Trains
In 2014, it was reported, ‘If all goes to plan, early next year a 32,000-tonne freight train laden with iron ore will roll out from a Rio Tinto mine site in the Pilbara region, bound for the port of Dampier 300km away on the West Australian coast. ...The big difference in 2015 is that instead of an onboard driver, the train will be remotely controlled by an operator sitting in a Perth control room 1500km to the south. After months of trials with driverless trains, Rio Tinto plans to begin scheduled operations next year as part of its “Mine of the Future” automation program’9. There were delays, but the ambitious $300 million research program has begun to pay dividends. In July 2018 it was reported that Rio’s “autonomous train, consisting of three locomotives and carrying around 28,000 tonnes of iron ore, travelled more than 280 kilometres from Rio Tinto’s mining operations in Tom Price to the port of Cape Lambert10. It was monitored but not controlled remotely. The national regulatory body—“The Office of the National Rail Safety Regulator” provided final approval.
Speaking to a number of people in Canada there was scepticism about the applicability of the technology in Canada because of the difficulties of port access and problems of cold weather. However, the productivity improvements gained from this technology will put considerable pressure to the global mining industry wherever it is applied. As a result of its innovation, Rio’s cost curve is the lowest of the major iron ore miners. In the podcast “Elements” on the BBC, a spokesperson for Rio Tinto estimated the company’s cost per tonne at $1711. At about the same time the commodity price was USD$5212. Verifying such boasts is hard, and comparing it against other actors which view such data as commercially sensitive virtually impossible.
Data Mining
Before explaining the trajectory of Rio Tinto’s data centres, it is important to give some context. Australia is an important global centre for mining software.
Exploration and mining software (EMS) has been a hugely innovative and an important segment of Australia’s $90 billion mining equipment, technology and services (METS) industry. (Austrade 2013) The segment of technology companies includes at least 50 dedicated firms based on two sub-segments: (1) information technology, and (2) specialised equipment (control, scanning, simulation and mineral processing technology). In 2012, these firms had total IT related sales of more than $1 billion, of which almost 50 per cent were exports, and employed an estimated 6,000 people. (Don Scott-Kemmis 201313) The sector is concentrated in Western Australia and Queensland (45 per cent and 30 per cent of firms, respectively)14.
With this background, it is understandable that Rio Tinto has established its data centres in Perth (Western Australia) and Brisbane (Queensland). The Perth Centre is an operations hub that oversees all Rio’s autonomous operations in Western Australia. Operators in Perth can take control of individual vehicles if necessary. But otherwise a more apt description is that the centre functions more like an air traffic control centre than a hands-on operational facility.
The Brisbane centre oversees all Rio’s operations globally. Rio Tinto claims that five per cent of all energy usage on the planet is used in crushing rock. The Brisbane big data centre in real-time monitors all rock-crushing activities in search of new efficiencies. As rocks of different grades pass through the processing facilities, the equipment can be fine-tuned to deal with different types of rocks, whether harder or softer.
Productivity
The question this technology raises is does it matter? Costly, yes. Definitely “cool” in a technological sense. But does it improve productivity?
Across economics, productivity is considered crucial to sectoral success. If we examine the Australian data we can see some interesting productivity trends. Typically, people like to focus on labour productivity. We can compare Australian mining and agricultural productivity for some relativity, but international comparisons get more difficult. Agricultural productivity in Australia has been steadily growing since 1990.
Mining productivity had been declining in Australia, from approximately 2000 through to 2011-12. From there it stabilised, and since has been improving. While it is not possible to attribute this purely to the introduction of new technology, the timing of technological innovation and rising productivity is aligned.
Figure 1: Australia: Labour Productivity Indexes - Quality-adjusted hours worked basis (2016-17 = 100)
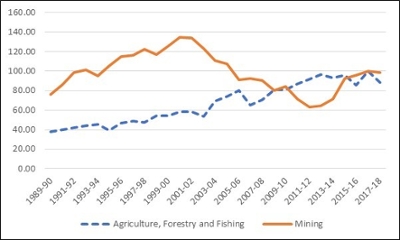
The Policy Issues
It is 10 years since the mining technological revolution started in Australia. However, this transformation should be understood as a peculiar 21st century innovation category—namely surprise disruptive technology.
In papers throughout the 2000s, including Ph.D. work submitted in 2003, there is no hint of the Autonomous Haul System emerging. The best estimate of where innovation was headed was in mine operations and value-added services16, such as software (which Australia has a very significant global slice). It was, therefore, a surprise when Rio launched its ‘mine of the future’ project. It is a pattern that has repeated itself in a number of domains, autonomous cars being a good example. Perhaps we should begin to expect this pattern.
For many managers and others in the mining industry, as well as a few observers outside the industry, the importance of innovation and new technology has long been recognized. For the most part, however, government officials and the general public consider mining to be a mature industry with relatively stagnant technology, where competitiveness depends largely or entirely on a country’s mineral endowment. However, the reality is that significant innovation in mining has been underway for decades. Specifically:
- Komatsu began work in Australia in the early 1990s on automated haulage systems;
- In 2005 it commenced new trials at Codelco’s Radomiro Tomic open-pit copper mine in Northern Chile;
- In 2008 Rio commenced a trial of 12 autonomous haul trucks;
- There is a clear and on-going trajectory of innovation, with a largely autonomous mining equipment region in the Pilbara now underway; and,
- The shift to move to underground autonomous mining is beginning to become apparent.
The fact is an incredibly rapid movement to autonomous activities has taken many by surprise, even going unrecognised as it was happening. But as with the application of all innovative and transformative change, economic and social policy issues emerge, as were laid out by Bellamy and Pravica17.
Balch says much the same thing18.
The idea of 21-century mines being run from centralised control centres far from the dust of the coalface has several significant selling points. Automation is arguably greener, safer and—after the initial up-front investment—has cheaper running costs. Mineworkers, local suppliers and government tax agencies are justified in being a tad sceptical, however. More robotic technology potentially means fewer low-skilled workers, less local contracting and lower mine-related tax receipts. “If you’re moving from mines that employ 5,000 to 10,000 people down to 500 or 1,000, then you’re obviously not going to get the same amount of local jobs,” says Howard Mann19, senior adviser on international law at International Institute for Sustainable Development (IISD) and co-author of a recent study on the impact of automation in the mining sector.
Contemporary mining in Australia and Canada utilises very significant fly-in and fly-out workforces. As numbers decline due to innovative and disruptive technology, the economic effects will reach into unexpected corners of both countries. Data for Canada20 suggest that a high percentage of FIFO workers in the oil sands live in British Columbia and the Maritime Provinces. It is likely, however, that British Columbia and the Maritime Provinces are not modelling the impact of job losses in Alberta.
By contrast, operating centres of the second economy follow traditional innovation rules of trajectories and clustering. All the data centres currently established in Australia are exactly where you would expect them to be—next to the existing centres. In Canada, the highest concentration of IT talent is probably Calgary, not Toronto, as Cooper Langford (see e.g. 201421) has pointed out. Thus, when mining data centres are established in Canada the most likely sites will be in Calgary.
It might seem that conversations around futuristic concepts such as the second economy of mining are premature in Canada. However, policy dimensions are complex with the trade-offs between social licence, First Nations involvement and taxation structures. The point is that the earlier provincial, federal and communities begin discussing the digital future, the more chance there is of getting the policy settings pointing in sound directions.
References
1 W. Brian Arthur (2011) ‘The second economy’ McKinsey Quarterly, October 2011.
2 P. 5 Economic Strategy Tables, Resources of the Future
3 Kathryn Diss Driverless trucks move all iron ore at Rio Tinto's Pilbara mines, in world first. Updated Sun 18 Oct 2015, 3:51pm http://www.abc.net.au/news/2015-10-18/rio-tinto-opens-worlds-first-automated-mine/6863814
4 Ibid.
5 The West Australian 6 July 2017 3:00PM https://thewest.com.au/news/wa/nobody-at-the-wheel-at-bhps-jimblebar-iron-ore-mine-site-ng-b88529442z
7 http://www.riotinto.com/australia/pilbara/mine-of-the-future-9603.aspx
8 https://www.mining-technology.com/features/mining-robots-rio-tinto-doubles-autonomous-drilling/ Accessed 2019-04-25
9 Geoff Hiscock, The Australian, October 15, 2014 12:00AM http://www.theaustralian.com.au/business/powering-australia/rio-rolls-out-the-robot-trucks/news-story/8068d1b8f5cb44eff811b4307cd80917
10 Read more at https://www.businessinsider.com.au/rio-tinto-robot-iron-iron-ore-2018-7#cLUREcA3qIJv7rpW.99
11 https://www.bbc.co.uk/programmes/p02rqfk1
12 https://www.indexmundi.com/commodities/?commodity=iron-ore&months=60
13 Scott-Kemmis, D. (2013) ‘How about those METS? Leveraging Australia’s mining equipment, technology and services sector’, Minerals Council of Australia.
14 Austrade (2013) Mining Software and Specialised Technologies.
15 Australian Bureau of Statistics (2018) 5260.0.55.002 Estimates of Industry Multifactor Productivity, Australia. Released at 11:30 am (Canberra time) 3 December 2018.
16 This includes research work I was involved with and since the early 1990s, I had taken an interest in the Australian mining industry due to my Australian government employment in areas related to science and technology policy and analysis.
17 Bellamy, D. and Pravica, L. (2011) ‘Assessing the impact of driverless haul trucks in Australian surface mining’ Resources Policy 36 (2011) 149–158.
19 Cosbey, A., Mann, H., Maennling, N., Toledano, P., Geipel, G. and Brauch, M.D. (2016) Mining a Mirage? Reassessing the shared-value paradigm in light of the technological advances in the mining sector. International Institute for Sustainable Development.
20 Mining in Canada’s Oil Sands: Labour Market Trends and Human Resources Challenges 2013.
21 Langford, C. Li, B. and Ryan, C. (2014) ‘Firms and their problems: Systemic Innovation and related diversity in Calgary’ in Innovating in Urban Economies: Economic Transformation in Canadian City-Regions. pp151-172. in Wolfe, D. University of Toronto Press.
Brian Wixted
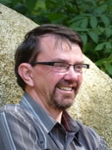
Brian Wixted, is an Adjunct Professor with the Johnson Shoyama Graduate School of Public Policy and the Centre for the Study of Science and Innovation Policy. During the 1990s, Brian worked for the Australian government on measures of innovation and agricultural science policy. In the early 2000s, he worked for a university research centre (AGEIS at what is now called Western Sydney University). Since moving to British Columbia in 2004, Brian has been involved in research projects on clusters and city innovation systems in Canada, research system evaluations and much more. He is currently finishing up research on digital technology adoption in prairie agriculture.